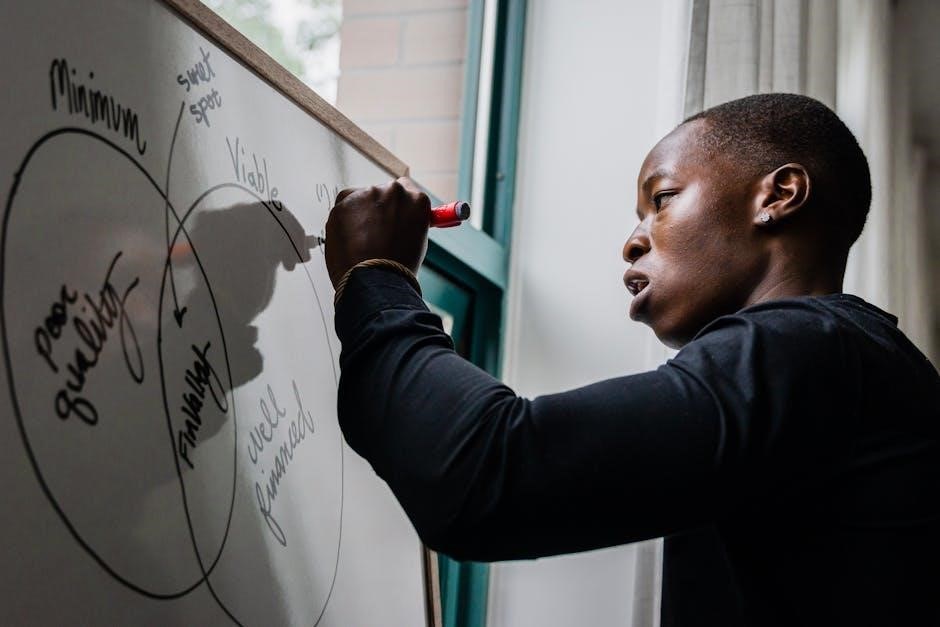
Work instructions are detailed, sequential steps guiding employees to complete tasks efficiently, ensuring consistency, compliance, and accuracy in workplace processes. They are essential for training, onboarding, and maintaining operational standards across various industries.
1.1 Definition of Work Instructions
Work instructions are clear, step-by-step guides detailing how to perform specific tasks; They outline necessary tools, materials, and safety measures, ensuring consistency and compliance. These documents are essential for standardizing processes, reducing errors, and training employees effectively across industries, from manufacturing to healthcare.
1.2 Importance of Work Instructions in the Workplace
Work instructions ensure consistency, reduce errors, and enhance productivity by providing clear guidance. They standardize processes, making training easier and improving compliance with regulations. By outlining expectations, they empower employees to perform tasks confidently, contributing to operational efficiency, quality, and safety across industries, from manufacturing to healthcare.
Key Elements of Work Instructions
Work instructions include clear purpose, defined responsibilities, step-by-step procedures, and visual aids to ensure tasks are performed accurately and efficiently, promoting consistency and compliance.
2.1 Purpose and Scope
The purpose of work instructions is to outline the objectives and boundaries of a task, ensuring clarity on what needs to be accomplished. The scope defines the range of activities, responsibilities, and deliverables, providing a clear framework for employees to follow, which helps in maintaining focus and achieving desired outcomes efficiently.
2.2 Responsibilities and Accountability
Work instructions clearly define roles and responsibilities, ensuring accountability at each step. They specify who is responsible for task execution, oversight, and compliance, fostering a culture of ownership and transparency. This clarity helps prevent errors, ensures adherence to standards, and maintains operational integrity by assigning clear duties and expectations to individuals or teams involved.
2.3 Step-by-Step Procedures
Work instructions provide detailed, sequential steps to complete tasks, ensuring consistency and accuracy. They outline specific actions, tools, and methods, minimizing errors and variations. By breaking processes into manageable steps, they simplify complex tasks, making them easier to follow and execute, while ensuring compliance with established standards and protocols. This structured approach enhances efficiency and reduces misunderstandings.
Benefits of Implementing Work Instructions
Work instructions promote consistency, compliance, and efficiency. They reduce errors, enhance training, and ensure processes are followed accurately, leading to improved productivity and better workplace outcomes.
3.1 Standardization of Processes
Work instructions ensure consistent execution of tasks across teams, reducing variability. By following clear, predefined steps, employees maintain uniformity in processes, enhancing quality and compliance. Standardization fosters operational efficiency, reduces errors, and ensures everyone understands expectations, leading to predictable and reliable outcomes. This consistency is vital for scalability and maintaining high standards across organizations.
3.2 Compliance with Regulations
Work instructions play a crucial role in ensuring compliance with industry regulations and legal standards. By outlining mandatory steps and safety protocols, they help organizations meet regulatory requirements, reducing legal risks. Clear instructions ensure adherence to quality standards, safety measures, and environmental guidelines, promoting accountability and audit readiness. This fosters a culture of compliance, safeguarding both employees and the organization.
3.3 Enhanced Training and Onboarding
Work instructions significantly enhance training and onboarding by providing clear, step-by-step guidelines for new employees. This structured approach reduces the learning curve, ensuring quick proficiency. Detailed instructions minimize errors, allowing trainees to understand expectations and perform tasks confidently. They serve as a consistent reference, fostering a smooth transition into the workforce and improving overall team performance efficiently.
3.4 Improved Efficiency and Productivity
Work instructions streamline tasks by providing clear, actionable steps, reducing errors and saving time. Employees can complete jobs more efficiently, knowing exactly what’s expected. Standardized processes minimize confusion, allowing teams to focus on high-priority tasks. This consistency ensures workflows remain smooth, boosting overall productivity and enabling employees to achieve their goals effectively and consistently.
Best Practices for Creating Work Instructions
Use clear, simple language and visuals like images or diagrams. Ensure instructions are user-friendly and accessible. Regularly test and update them with feedback from employees to improve accuracy and relevance.
4.1 Clarity and Simplicity
Work instructions must be clear and simple to ensure understanding. Avoid jargon and complex sentences. Use concise language and straightforward steps. Ensure each instruction is easy to follow, minimizing confusion. This promotes efficiency and reduces errors, making tasks more manageable for employees.
4.2 Use of Visual Aids
Incorporating visual aids like diagrams, flowcharts, and images enhances understanding. They break down complex steps, making instructions more engaging and accessible. Visuals help employees quickly grasp processes, reducing training time and errors. This approach is particularly effective for diverse workforces or tasks requiring precision.
4.3 Regular Reviews and Updates
Regularly reviewing and updating work instructions ensures they remain accurate and relevant. This process helps identify outdated practices, incorporates feedback, and aligns with new regulations or technologies. Updates should be clearly communicated to all stakeholders to maintain consistency and compliance. This proactive approach enhances efficiency and supports continuous improvement in workplace processes.
Common Pitfalls to Avoid
Common pitfalls include overly vague instructions, lack of necessary details, and inadequate training, leading to confusion and errors. Regular reviews help mitigate these issues effectively.
5.1 Overly Vague Instructions
Overly vague instructions lack specificity, leading to confusion and inconsistent task execution. They fail to provide clear expectations, resulting in misinterpretation and variability in outcomes. Vague instructions hinder effective training and reduce workplace consistency, making it difficult for employees to understand their responsibilities and perform tasks accurately. Clarity is essential to avoid errors and ensure compliance.
5.2 Lack of Necessary Details
Lack of necessary details in work instructions can lead to confusion, errors, and non-compliance. Missing specifics, such as required tools or safety protocols, can compromise task execution and workplace safety. Employees may rely on assumptions, reducing efficiency and accuracy. Detailed instructions ensure clarity, consistency, and adherence to standards, preventing misunderstandings and promoting high-quality outcomes. Regular reviews can help identify and address gaps in information.
5.3 Inadequate Training on Work Instructions
Inadequate training on work instructions can lead to misunderstandings, errors, and non-compliance. Employees may struggle to follow procedures correctly, especially if they lack prior experience or clarity on expectations. This can result in inefficiency, safety risks, and poor-quality outcomes. Effective training ensures that all team members understand and can apply the instructions accurately, fostering consistency and operational excellence across the organization.
Role of Technology in Work Instructions
Technology enhances work instructions by providing digital documentation, real-time updates, and integration with workflow systems, ensuring accessibility, consistency, and efficiency in operational processes across organizations.
6.1 Digital Documentation Tools
Digital documentation tools streamline the creation, storage, and dissemination of work instructions. They offer templates, collaboration features, and version control, ensuring accessibility and consistency. Cloud-based solutions enable real-time updates, reducing errors and enhancing compliance. These tools also support search functionality, making it easier to locate specific instructions, thereby improving efficiency and productivity across organizations.
6.2 Workflow Management Systems
Workflow management systems enhance task execution by integrating work instructions, offering task assignments, notifications, and progress tracking. They ensure adherence to procedures, reduce errors, and improve efficiency. By embedding instructions directly into workflows, these systems provide clear guidance, enabling employees to perform tasks accurately and consistently, which benefits organizations through increased consistency and regulatory compliance.
Case Studies and Real-World Applications
Industries such as manufacturing and healthcare use work instructions to improve efficiency and compliance, reducing errors and enhancing training effectiveness across their operations.
7.1 Successful Implementation in Manufacturing
Manufacturing sectors have leveraged work instructions to streamline production processes, reduce errors, and ensure compliance with quality standards. By providing clear, step-by-step guidance, these instructions enhance employee training and efficiency, leading to higher product consistency and reduced downtime. This approach has been particularly effective in automotive and aerospace industries, where precision is critical.
7.2 Use in Healthcare for Compliance
In healthcare, work instructions are vital for ensuring compliance with strict regulations and protocols. They provide clear, step-by-step guidance for medical staff, minimizing errors and ensuring adherence to safety standards. Proper documentation and training are emphasized, reducing legal risks and maintaining patient trust.
Future Trends in Work Instructions
Future trends in work instructions include AI-driven automation, interactive formats, and real-time data integration, enhancing efficiency and user experience across industries.
8.1 Integration with AI and Automation
AI and automation are revolutionizing work instructions by enabling dynamic, real-time updates and personalized guidance. AI-driven tools can analyze workflows, optimize processes, and generate instructions tailored to specific tasks or user roles. Automation ensures consistency and reduces errors, while predictive analytics can anticipate challenges and provide proactive solutions. This integration enhances efficiency, scalability, and adaptability in modern workplaces.
8.2 Adaptive Learning Systems
Adaptive learning systems use AI to personalize work instructions, tailoring them to individual skill levels and learning paces. These systems analyze performance data, providing real-time feedback and adjusting training content accordingly. They enhance proficiency by focusing on specific weaknesses and strengths, ensuring a more effective and engaging learning experience that evolves with user needs and industry demands.
9.1 Recap of Key Points
Work instructions provide clear, structured guidance for tasks, ensuring consistency and compliance. They enhance procedural accuracy, reduce errors, and support training. By standardizing processes, they improve efficiency and productivity while maintaining operational and safety standards. Effective work instructions are vital for achieving organizational goals and ensuring high-quality outcomes across all levels of an organization.
9.2 Final Thoughts on the Importance of Work Instructions
Work instructions are fundamental for ensuring clarity, consistency, and compliance in workplace processes. They streamline tasks, reduce errors, and enhance productivity, serving as a cornerstone for effective training and operational excellence. By providing clear guidance, they empower employees to perform confidently, contributing to organizational success and maintaining high standards of quality and safety across all operations.